5 Common Tire Issues That Can Shut Down Your Fleet—Fast
Tire issues like underinflation, tread separation, and overloading are leading causes of fleet breakdowns—but nearly all are preventable. Learn the top 5 problems and how proactive maintenance with FleetTyre can help avoid costly downtime.
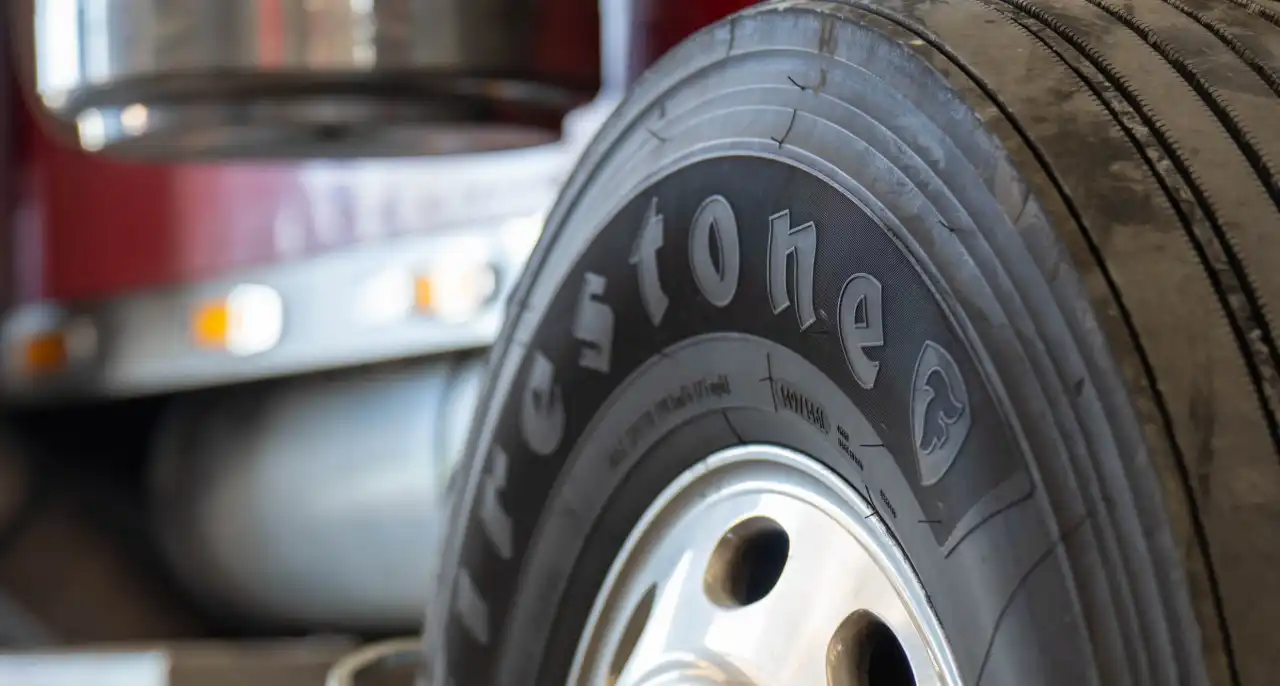
When you’re managing a commercial fleet, tire problems are more than just a minor hiccup—they're ticking time bombs. One failed tire can sideline an entire delivery, delay your entire schedule, and run up costly emergency service calls. And while some issues happen suddenly, most are preventable with the right knowledge and a consistent maintenance plan. Let’s break down five of the most common tire problems that can bring your fleet to a grinding halt—and what you can do to keep that from happening.
Fleets With Underinflated Tires
Underinflated tires are easily the most overlooked issue, but they’re also one of the deadliest. A tire that’s just 20% under its recommended PSI is considered flat by commercial standards. When tire pressure drops, the sidewalls flex more than they’re designed to, building up excessive heat and weakening the internal structure. Over time, this leads to tread separation, blowouts, or worse—catastrophic tire failure at highway speeds.
The impact doesn’t stop at safety. Underinflated tires also force your engine to work harder, increasing fuel consumption. If you’re running a full fleet, that inefficiency adds up fast. And in colder climates or seasons, pressure drops quickly due to temperature fluctuations. That's why regular pressure monitoring isn't a luxury—it's a necessity.
How to prevent underinflation:
- Use tire pressure monitoring systems (TPMS) to automatically alert drivers and dispatchers.
- Train operators to visually inspect tires daily and follow up with manual pressure checks weekly.
- Establish a monthly fleet-wide tire pressure inspection routine.
- Adjust pressure according to seasonal temperature shifts or altitude changes.
Tread Separation
Tread separation might look like a cosmetic issue at first, but don’t be fooled—it’s often a prelude to total tire failure. This happens when the tread layer begins to peel away from the tire casing, usually caused by excess heat, improper repairs, or poor bonding in retreaded tires. Once that separation begins, the structural integrity of the tire is compromised, and the risk of blowout skyrockets.
On a loaded semi traveling 65 mph, a tire blowout doesn’t just mean downtime. It’s a safety hazard for the driver and everyone else on the road. In severe cases, the whipping tread can even damage air lines, fenders, or other adjacent components. For fleets operating in hotter climates or mountainous terrain, the risk is even greater due to increased road friction and heat.
What to watch for and do:
- Look for signs of bubbling, cracking, or uneven rubber texture during every pre-trip inspection.
- Avoid using off-brand or cheap retreads without proper bonding certifications.
- If using retreaded tires, ensure they’re inspected more frequently, especially during warmer months.
- Replace tires near the end of their service life—even if they look fine from the outside.
Uneven Tire Wear
Uneven wear on a tire is usually a symptom of a deeper mechanical issue. It could be misalignment, bad shocks, or even improper tire balancing. When tires wear unevenly, the contact patch changes, which compromises handling, stability, and braking performance. Worst of all, the damaged section of the tire is often on the inside edge, hidden from view.
This kind of wear leads to more frequent tire replacements, but that’s only the beginning. It increases vibration, which can stress suspension parts, wheel hubs, and even your drivetrain. And over time, the uneven forces can snowball into more significant mechanical failures. Don’t overlook that wavy tread pattern or slightly bald shoulder—it’s a warning sign.
How to keep wear patterns even:
- Schedule wheel alignments every 25,000 to 30,000 miles or after any suspension work.
- Rotate tires every 6,000 to 8,000 miles to balance wear between drive and steer tires.
- Inspect suspension components like shocks and bushings for damage or excessive play.
- Use digital tread depth gauges to record wear trends across the fleet.
Overloading Your Fleets
Your tires are only rated to carry so much. When you push past those limits—even unintentionally—you run the risk of structural failure. Overloading causes extreme pressure on the tire casing, especially on the sidewalls. This leads to heat buildup, rapid wear, and, eventually, casing distortion or full blowout.
Ignoring load limits exposes your entire fleet to roadside violations, fines, and liability issues. This is especially true when navigating hilly or hot environments where additional strain is placed on the tires.
Overloading prevention strategies:
- Always check each tire's load index rating and match it to your Gross Axle Weight Rating (GAWR).
- Use on-board scales or axle weight sensors to monitor load distribution.
- Provide regular driver training on proper loading techniques and weight limits.
- Consider upgrading to higher-rated tires for trucks that frequently operate near capacity.
Bead Damage
Bead damage is a lesser-known issue, but it’s just as dangerous as a sidewall puncture. The bead is the part of the tire that seals against the rim, and if it’s compromised, your tire won’t hold air properly. This can lead to slow leaks or even a sudden loss of pressure while driving. Bead damage often goes unnoticed until the tire completely separates from the wheel.
Most bead damage occurs during tire changes or improper mounting using the wrong tools. But it can also happen from curb strikes, hitting potholes too hard, or even incorrect inflation practices. Once damaged, a tire’s bead can’t be repaired and must be replaced entirely. For fleets with frequent tire swaps, this risk is even higher.
Bead protection tips:
- Always use professional-grade tools and trained technicians for mounting and dismounting.
- Avoid makeshift field repairs or curbside remounts whenever possible.
- Instruct drivers to steer wide of curbs, especially in urban areas.
- After a blowout or major road impact, inspect the rim and bead for signs of damage before installing a new tire.
Don’t Let Tire Failures Halt Your Operations
Tires might not be the most glamorous part of your fleet, but they’re among the most critical. Underinflation, tread separation, uneven wear, overloading, and bead damage are all common issues that can escalate into full-blown emergencies if ignored.
With FleetTyre Commercial Truck Service, understanding the causes and being proactive with inspections, training, and maintenance can keep your rigs rolling, reduce repair costs, and stay ahead of costly downtime. When it comes to tires, prevention is the best cure. A bit of attention today can save you thousands tomorrow.
Contact Us
Need roadside assistance, have questions, or want to schedule your truck or trailer in for a service or repair? Get in touch, we're open Monday through Friday 8:00am to 5:00pm and have roadside assistance available 24/7!